Tricycle Conceptual Design
January 30, 2014
The team has been hard at work over the last week nailing together the conceptual design for our recumbent tricycle. We first broke into a number of task forces. One group is working on designing the carbon fiberfairing for the vehicle and looking at our overall testing and analysis plan. The second group is designing the front wheel frame and steering mechanism for the vehicle. The third group is designing the drivetrain and specifying the components which we will buy. Finally, a group is investigating the possibility of building a fabric fairing in the future.
Fairing Design & Analysis
Our fairing and testing group began by determining our goals for the vehicle. Although our fairing last year was very aerodynamic, the bicycle had stability issues with some riders and it was not comfortable for all of our team members. This year, we want to build a vehicle that is more stable, easy and comfortable to ride while keeping our aerodynamic losses as low as possible (ideally no worse than last year's vehicle) - a challenge with the larger frontal area inherent of tricycles.
The first question to answer was whether or not we wanted our two front wheels within the main fairing of the vehicle. Although having one fairing is simpler, having the wheels outboard has the possibility to reduce the frontal area of the vehicle, simplify manufacturing and allow for a wider wheelbase, improving stability.
We were also intrigued by the wheels (with wheel fairings) acting as stabilizing fins to improve vehicle handling. This decision was also affected by the steering team's conclusion that over-the-seat steering was a feasible steering method. If under-the-seat or direct knuckle steering was deemed necessary, the increased frontal area of the main fairing could almost encapsulate the wheels.
Next, we moved on to look at rider position within the vehicle. Looking back at our past year's design reports, we found that our prior testing has shown that the rider can comfortably ride and provide power at angles down to 20° from horizontal. We agreed that by using thinner plastic, we could make a wide enough window (with carbon ribs crossing it) so that visibility would not be an issue at any angle. With this knowledge, we agreed to lower the rider position so that the feet and knees were the limiting height factor of the vehicle rather than the head. We will make extensive use of side windows to make this work.
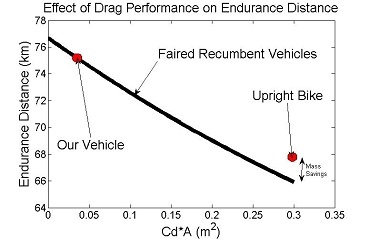
Also on the fairing team, we have jumped straight into analysis. We have been using STAR-CCM+ to check the aerodynamic performance of each of our design concepts and have been iteratively working through them. Furthermore, we have built some computer models of how the aerodynamics of the vehicle will affect our performance at competition. We have found that both weight and aerodynamics are very important factors - in fact, aerodynamics has shown to be more important than we previously thought. A plot of our expected endurance distance traveled against our fairing coefficeint of drag is shown at left. As shown, although an upright bike has a higher coefficient of drag than one of our vehicles, its lighter weight still makes it competitive. However, our fared vehicles should perform better than an upright bike on both the sprint and endurance races due to their improved aerodynamics, even at a weight penalty.
So overall, we will be building a small narrow fairing for the rider to sit within. Our wheels will be outboard of the fairing and will have their own mini-fairings. We hope to finish detailed design in the next week and move into manufacture.
Drivetrain
The Drivetrain team has been hard at work designing the cranks, gearing and supports for the 2014 competition vehicle's drivetrain.
We began our design sprint by asking if the adjustable pedal systems we have embraced in the past two years are necessary. While they do a great job compensating for our wide range in riders, the large window design and lack of head 'bubble' in the current fairing model would allow for riders to move slightly within the fairing while maintaining visibility and not reducing aerodynamics. Furthermore, moving the rider could dramatically simplify the drivetrain.
We proceeded to investigate a swing arm style adjustable pedals system, similar to that featured on our leaning tricycle from last semester. We found that the swing arm took up a very large volume within the fairing, making it somewhat undesirable from an aerodynamics point of view. Furthermore, the parallel bar design we have used in years past has so many machined parts that we were looking to move away from it. Because of this, we decided to move to fixed pedals configuration. We plan on having a fixed seat and using various molded seat pads to allow different riders to ride the vehicle. The configuration of these pads is to be determined. This has the added advantages of reducing the number of mechanical components which could fail (last year, we had a major drivetrain failure during competition) and simplifying the whole vehicle.
Once this decision was made, the drivetrain looked to design the parts for our vehicle drivetrain. We have decided to keep with custom cranks due to reduced q-factor (distance between pedals), allowing for a narrower fairing. We will return to clamping the cranks onto the cranks to reduce slop over last year's retaining ring and hex shaft method. We are still investigating whether or not we want to replace the traditional bicycle bottom bracket with a custom machined bearing holder - the advantages and disadvantages of this will be explored in the next week.
Finally, we started picking and purchasing parts for the vehicle. We have bought our wheel hubs, the metal tube for the frame, brazing rod and more. Team members have also been hard at work picking wheel rims and tires. This will continue in the next week.
Front Wheels & Steering
Our third team, the front wheel and steering team, has been working on designing the frame to hold our front wheels, the associated wheel shafts and knuckes and the steering geometry and linkages. Over the past week, they have done quite a bit of research and have been looking into Ackerman steering geometry with help from Chris of Olin's Mini Baja team.
On the steering side, we are currently looking at having a bent steering column with a u-joint at the bend. This will allow us to fit all of our riders in the vehicle while not bumping into them between their legs. Over the next week, the team will finalize its frame design and the design of all of the individual parts so we can move into manufacturing soon.
Rear Wheel Mounting
A small group has also been hard at work figuring out how to mount our rear wheel to the monocoque fairing.
We are currently looking at a number of options for how to bolt into the monocoque so that the rear wheel is removable. We are looking to last year's design for inspiration but are worried about increased loading due to the chain given that this is now our drive wheel. The rear wheel mounting solution also needs to stay clear of the deraileur. Overall, we are still evaluating some preliminary designs here in comparison to past years and will look at picking a design soon. We hope to balance strength and manufacturability with a design that will be able to compensate for differences between the fairing CAD model and the actual fairing to allow for easier integration down the road.
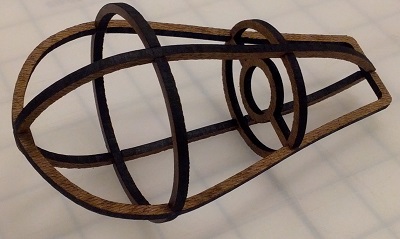
Fabric Fairing
Finally, we have a group that has been investigating using fabric as a fairing material. Fabric has the advantage of weight which could offset any aerodynamic losses. We have made several laser-cut skeletons which we will strech various fabrics over and perform wind tunnel testing to see how they perform against a reference sample of carbon fiber. This is still very much a research & development project and we're not sure if this will end up on the competition vehicle. However, we are very excited by the possibility and will continue to investigate it in coming weeks.
Overall, everything is really coming together. We're all excited for how this vehicle is coming and will have more to show next week at our design review.