Two Weeks Down
February 1, 2013
As January comes to a close, we've made a lot of progress over the first two weeks of the semester. We've been hard at work on everything from landing gear design to fairing manufacture.
The fairing plug has been routed. After three busy days of cutting on the off-campus CNC router, we have cut all 54 slices necessary to make our foam plug. However, the plug is far from complete. We still need to sand it flat, apply spackle and bondo to touch-up areas, paint it and wax it before we can make our female mold. We will continue to work on the plug in the upcoming weeks.
We recently recieved a generous donation of carbon fiber from one of our sponsors, Kazak Composites but still need to procure many of the other materials necessary for manufacture.
In addition to work on fairing manufacture, we've been working on a number of design tasks. For one, we have been working to shape our fairing's window, which has significantly more curvature as designed than any of our previous vehicles. Without molding, which we fear would make the window less optically transparent, our shapes are limited to conical sections which can be curved and knife-edge bends from our sheet metal brake. Progress has been made with transforming the curved shape into a close approximation which can be manufactured with bends and conical sections. We hope to finish this design in the upcoming week so that we can cut our window either by hand or with the Olin Machine Shop's waterjet cutter.
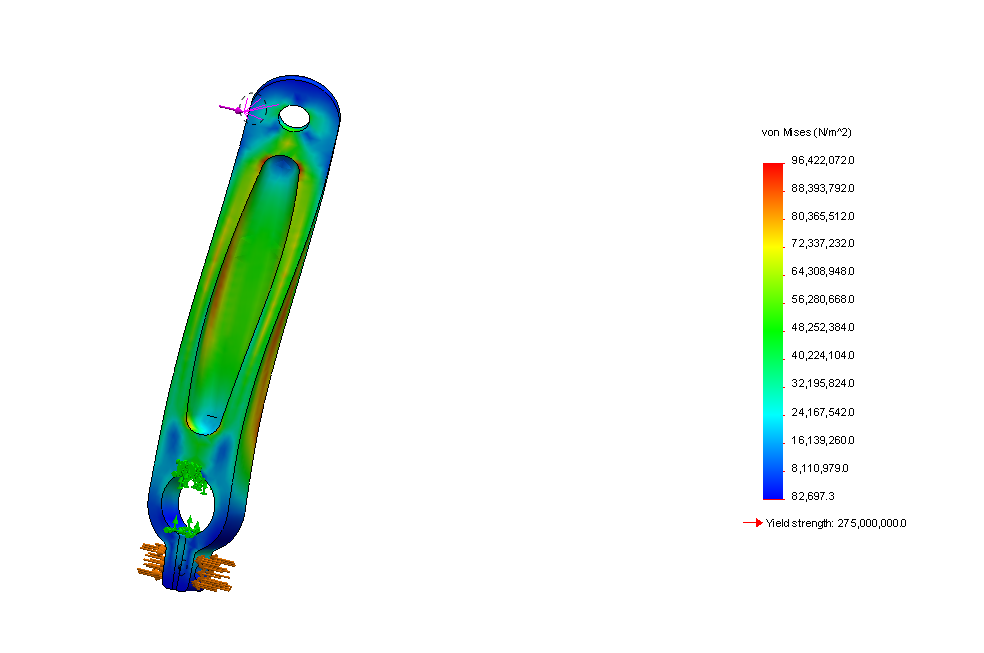
Crank finite element simulation results
We've also been looking at designing the doors and access panels for the fairing so that we will be able to easily enter and exit the fairing as well as work on the vehicle. We have some concepts which we are happy with but will continue to refine the design in the coming days.
One of our major design goals for this year was to lighten the vehicle as a whole. One of our strategies towards this has included looking at redesigning a number of machined components to be more weight optimized. We've been using finite element simulation, as shown in the graphic at left. Other strategies include better planning of carbon fiber lay ups to reduce use of unnecessary material.
The landing gear prototype which was illustrated in an earlier blog post was built and it was determined that unplanned friction in the actuating cables prevents it from sucessfully deploying the landing gear in a timely fashion. A redesign is in progress and is almost complete; it will be detailed in a later post.