Fairing Cutting Starts
January 25, 2013
Today, we began cutting the foam plug for our aerodynamic fairing, one of the main subsystems of our vehicle. Making the fairing is a very time consuming process and this marks the first step of the manufacturing process.
We begin by taking large (4' x 8' x 2") sheets of foam insulation and cutting them into rectangles. Each of the rectangles is then cut on a CNC Router to give it the precise shape necessary. The router takes multiple steps, which vary in size depending on the amount of curvature on the slices. We could make the steps all very small, but this would add significant time to the cutting process.
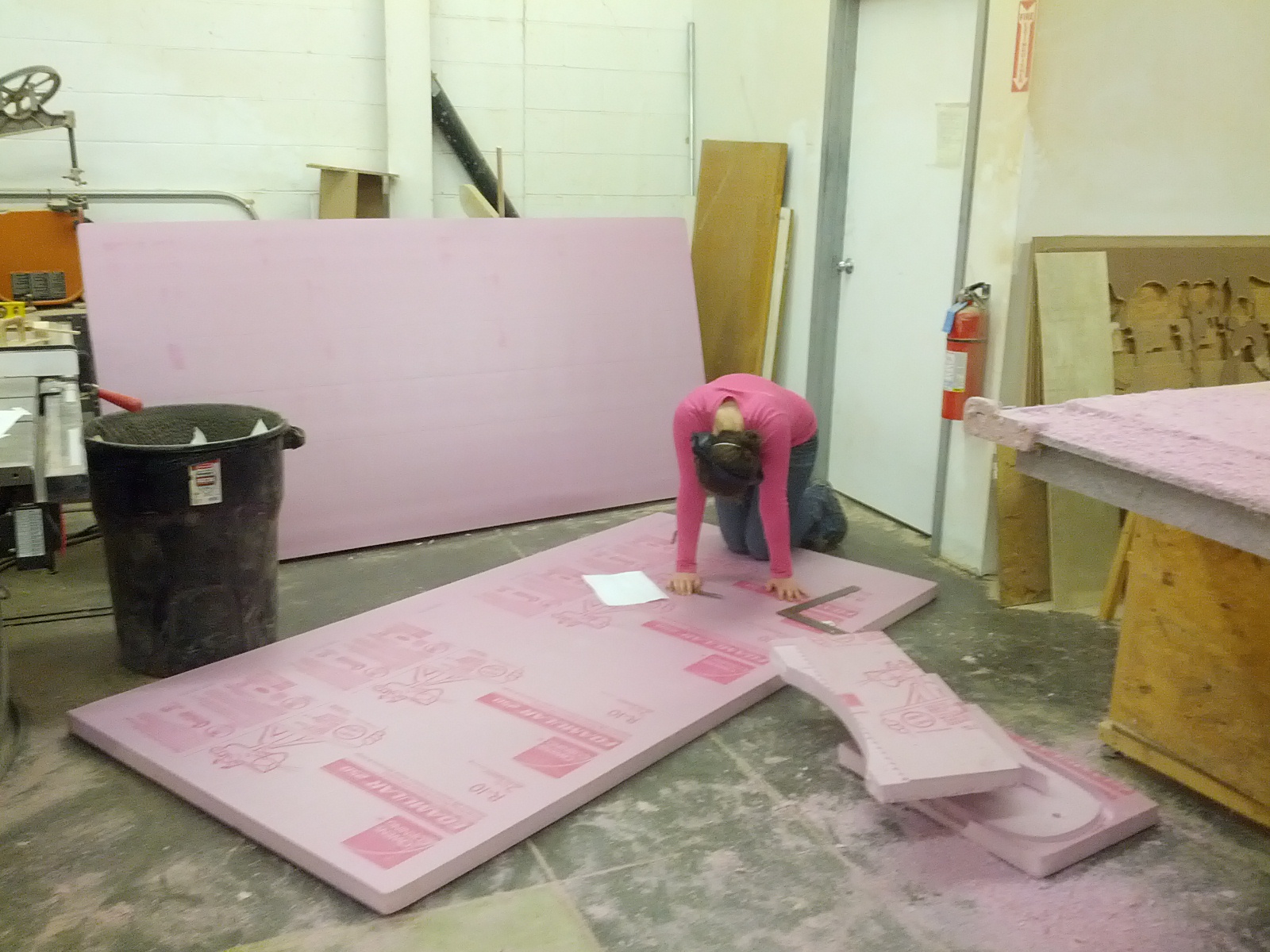
Slicing the foam into rectangles
Last year, we performed this process on a CNC router at Olin College which one of our professors had obtained for research. However, this router is currently out of service as it is being moved to a new location on campus.
This year, we decided to cut our fairing at a local Boston-area maker space instead of waiting for Olin's router to be set up. Although this is hard on our budget as it is not free for us, it allows us to keep to our tight schedule which is valuable in and of itself. Furthermore, this router is not as precise as the one we used last year and has more significant backlash and is slower.
Today, we spent approximately 9 hours at the shop cutting the fairing. We cut nineteen of the approximately fifty five slices of the fairing, slightly over one third. Although it is a slow and laborious process, it produces a nice and smooth plug which eases the later steps in the process.
After the plug is routed, it will be sanded, touched up with spackle and bondo and painted. It will be marked up into sections and we will lay up a multipart female fiberglass mold on top of it.
Once the multipart mold is constructed, we can then lay up the various parts of the carbon fiber monocoque fairing inside the female mold, giving us a great surface finish. This is a similar process to what we underwent last year, and more information can be found in our 2012 design report.

The finished slices